0 Preface
With the increasing living standards of people, the aging of China's population is becoming more and more obvious. As a kind of service robot, vacuum robot can replace people to clean some simple labor such as room, workshop and wall.
Making service robots have a broad market has become the focus of research by some enterprises and research institutes. At present, the vacuuming robots on the market are also intelligent, but most of them are costly due to unreasonable structure, poor versatility, and high integration, which is not conducive to popularization. Based on the research and summary of relatively mature products on the market, an indoor vacuuming robot with self-navigation function is designed based on ARM Cortex-M3 processor. The utility model has the advantages of compact shape, simple structure, stable operation, low noise, low cost, convenient operation, and an expandable interface, and the user can further develop its function according to actual needs.
1 Overall structure of the vacuuming robot
Designing a mobile cleaning robot for indoor use with the ARM Cortex-M3 processor, the main task is to be able to clean the room by itself, so the following functions should be available:
(1) can correctly judge the room in which the robot is located and the position in the room;
(2) It can correctly detect obstacles such as walls and furniture in the room;
(3) After completing the cleaning task in all rooms, you can return to the starting point and shut down.
In order to prevent the robot from stalling during work, and to freely enter some furniture such as sofas, tables, etc., the vacuuming robot can not be too high, and the shape is semi-cylindrical. The chassis is supported by four wheels, wherein the left and right sides are driving wheels, which are directly driven by two micro DC motors, and the front and rear two universal wheels serve as support and guide. Multi-sensor system is composed of collision, infrared sensor and ultrasonic. An infrared receiving sensor is arranged above the robot, and a proximity sensor is evenly distributed on the edge of the chassis for detecting obstacles; a collision sensor is installed in front of the robot; and an ultrasonic distance measuring sensor is arranged on the front and the left side to detect the surrounding environment.
The overall frame design is shown in Figure 1.

2 hardware main design
The hardware system is mainly composed of ARM Cortex-M3 processor, sensor module, motor drive module, human-computer interaction module and wireless remote control transmitter module.
2.1 ARM Cortex-M3 processing
The main task of the robot control system is to perform cleaning route planning, control cleaning and vacuuming mechanisms, and complete various control actions based on the feedback data from sensors and encoders. Design a suitable human-machine interface to display the robot status and running time on the LCD. Therefore, the robot control system includes a sensor module, a motor drive module, an infrared remote control receiving module, an LED indicator, and a liquid crystal display module. The ARM Cortex-M3 processor is used as the core of the robot control system, which is mainly low cost, small pin count and low power consumption, and has extremely high computing power and strong interrupt response capability, and the operating current is only 50 mA.
2.2 Motor Module
Divided into small motor drive circuit and two high-power drive boards, including two small DC motors for walking and high-power brushless DC motors for vacuuming, DC brush motors for sweeping, DC side brushes for sweeping corners Motor. Because the motor determines the walking path and vacuuming power of the robot, a special drive board is designed, as shown in Figure 2. The design of the walking module plays a vital role in the obstacle avoidance planning of the vacuuming robot. We design the vacuuming robot as a closed loop control, which mainly includes the driving circuit and the photoelectric encoding feedback circuit. The photoelectric code feedback circuit obtains the current motor speed by calculating the number and phase of the feedback feedback. The chip can drive a motor of up to 25 V. The working voltage of the walking motor in the vacuuming robot is 24 V. The voltage of the chip is 5 V. The PWM wave output from the chip is converted into a large voltage PWM wave control motor. The limit parameters are shown in Table 1.
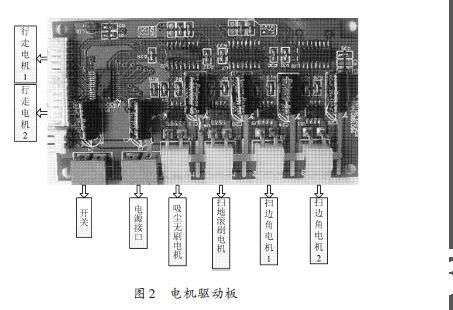
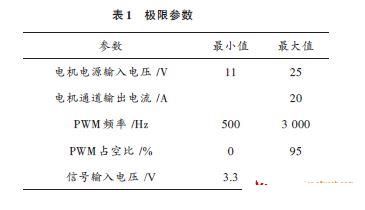
2.3 Sensor Module
It mainly consists of 3 parts: ultrasonic module for measuring and sensing obstacles, infrared and collision sensors, sensors for state detection (detecting battery power, dust bucket, motor stalling and floating). The sensor module enables the robot to make the right judgments about the surrounding environment and provide intelligent decisions for the successful completion of tasks.
(1) Ultrasonic ranging sensor module
Due to the working environment, indoor vacuuming robots must have obstacles for detecting various sizes, heights, and colors. Ultrasonic is a non-contact detection technology that transmits in the air without external factors such as light, smoke, and electromagnetic fields. Interference, compared with infrared sensors, ultrasonic sensors have longer sensing distances, higher reliability, and lower cost. Therefore, the detection of obstacles can be effectively performed using a high-precision ultrasonic ranging system.

In 2008,a new industrial park of Liandajin was built in Daya Bay National Economic Development Zone,huizhou with CNY120 million.The Park covers an area of 20000 square meters including 12000 square meters of manufacturing plant,The employees has been up to 1000 and the output has been 60000 square meters per month.
PCB,PCB Manufacturer,PCB Fabricator,Circuit Board,Printed Circuit Board
Huizhou Liandajin Electronic Co., Ltd , https://www.ldjpcb.com